AUTOMATIC FORMING MACHINE MMC-200
FOR PRODUCING THE PRODUCTS OF CEREAL MASS
In production the product, you can use various ingredients, for example, such as protein balls, puffed rice, coconut flakes, peeled sunflower seeds, dried apricots and other chopped dried fruits, crushed nuts, poppy seeds, whole kernel nuts, various cereals, balls, extruded products: corn, rice, protein, etc. Sublimated fruits, berries, crushed waffles, it all depends on your imagination and needs.
Syrup acts as a binder, and it is also possible to add honey, or condensed milk or chocolate, etc. Also you can use of sublimated syrups such as Molda 13.
Specifications
- Working width: 200 mm
- Roller Diameter: 250 mm
- Capacity: up to 5400 bars / hour *
- Energy Efficiency Class: IE 3
- Irrigation device: 1 pc.
- Tacts/min: 10-55
- Compressed air: 6 bar
- Weight: 220 kg
- Air consumption: ~70 l/min
- Electric power: 380 V, 50 Hz, 3 phases
- Dimensions LxWxH: 900х780х770 mm
- Fully automatic by touch screen panel
- * When calculating a bar size 95*30*15 mm
Advantages
Compact and high capacity of the forming machine MMC-200
Quick change of formats, and wide range of different formats and individual development for the client's product
A wide range of masses for forming
Easy service, the ability to integrate into an existing line
The ability to provide equipment for lease (for testing at the customer's enterprise)
Staff training and equipment launch
Logistic support (air, railway, car, sea)
Use of quality components
The samples of products
-
Contains B-group vitamins, many macro- and microelements, polyunsaturated fat, is a real source of energy.
Ingredients: sunflower seeds, black sesame seeds, flax seeds, sublimated raspberries, corn flakes, raisins, syrup with add honey.
-
The beneficial composition of this balls helps to reduce the acidity of the stomach, remove toxins from the body, and also restores energy, causes a surge of strength in the human body.
Ingredients: puffed rice, whole peanuts, raisins, dried chopped barberry, rye flakes.
-
The bar is enriched with protein and fiber. This makes it ideal for those who want to always monitor the state of their figure. And those beneficial substances that are in its composition positively affect the body as a whole.
Ingredients: Rice balls, candied fruits (pineapple), pumpkin seeds, wheat flakes, dried cranberries, chocolate, crushed hazelnuts.
-
It is rich in easily digestible protein, it contains dried blueberries - rich in vitamins, as well as sublimated strawberries, which prevents the formation of cancerous tumors and prevents the occurrence of anemia.
Ingredients: protein balls, oatmeal, dried blueberries, sublimated strawberries, raisins, Jerusalem artichoke syrup.
The technological process of work the forming machine MMC-200
Forming machine for cereal mass MMC-200 is very easy to operate and service. You will not need large production areas and huge lines. Despite its small size, the forming machine MMC-200 has capacity up to 5 400 bars per hour, with a working width of 200 mm.
The prepared mass (cereal mixed with syrup) is loaded into the hopper of the forming machine manually or automatically using a transport system. Special feeding shafts in the hopper of the forming machine fill the cells in the forming roll by cereal mass. Cells are made individually for each customer based on the size and shape of the final product. Then the stamp system gives the desired shape to the cereal mass.
Thus, the forming machine MMC-200 works without scraps and defects, and cereals are not damaged during forming. Control is carried out using the touch screen panel. The stamp system has adjustable parameters, such as pressure force (allows you to adjust the density of the final product), stamp pressure time (for different masses, different stamp pressure time may be required to forming). All parameter settings are saved in the recipe, which allows you to produce a large assortment of cereal masses with one forming machine. Experiment, find new combinations of taste and benefit, because the compositions of cereal masses can be a great many.
Next, the already formed product enters to the belt of the transport system of the forming machine. Thanks to the integrated transport system, the finished product can transferred to the enrobing or packaging machine.
The technological process of the automatic line
Step 1. Mixing the components. Cereal ingredients in accordance with the proportions of the formulation are loaded into the mixer MSW-90. Maked the mixing process. Then a binder (syrup) is added to the resulting mass and the mass is re-mixed to a homogeneous consistency. The resulting mass is unloaded and fed into the hopper of the forming machine for cereal mass MMC-200 using a transport system or manually.
Step 2. Forming. After loading the mass into the hopper of the forming machine MMC-200, maked the forming process and the product of the final form for the next process step according to the technology enters the machine conveyor belt. It can be: cooling (for solidification syrup); coating with chocolate or yogurt glaze (the whole product or only the bottom); heat treatment (on trays in a convection-type oven or by conveyor into a tunnel-type oven).
Step 3. Cooling. If the technology of the binder (syrup) requires cooling for further work, then the product after the conveyor belt of the forming machine goes to the conveyor of the cooling tunnel SW-CT 200, the working length is 10 m.
Step 4. Enrobing. If the product according to the technology needs to be enrobed with chocolate or any other glaze, then after the cooling tunnel or immediately after the forming machine MMC-200, the product enters the mesh tape of the SW-ET 200 enrobing machine, where the product is completely enrobing with chocolate or glaze or only the bottom of the product.
Step 5. Cooling. After the enrobing machine SW-ET 200, the product must be cooled. For this is used the cooling tunnel SW-CT 200 , the working length 10 m.
Step 6. Packing. After all the processes according to the technology are finished, the product can be packaged. The most popular type of packing for this kind of product is flowpack packaging. To automate the packaging process, as well as to increase the speed of packaging, is used the automatic packing machine PMW-250 with automatic feeders, which align the product from the production line to one stream. The packed product is ready for sale.
Pictures
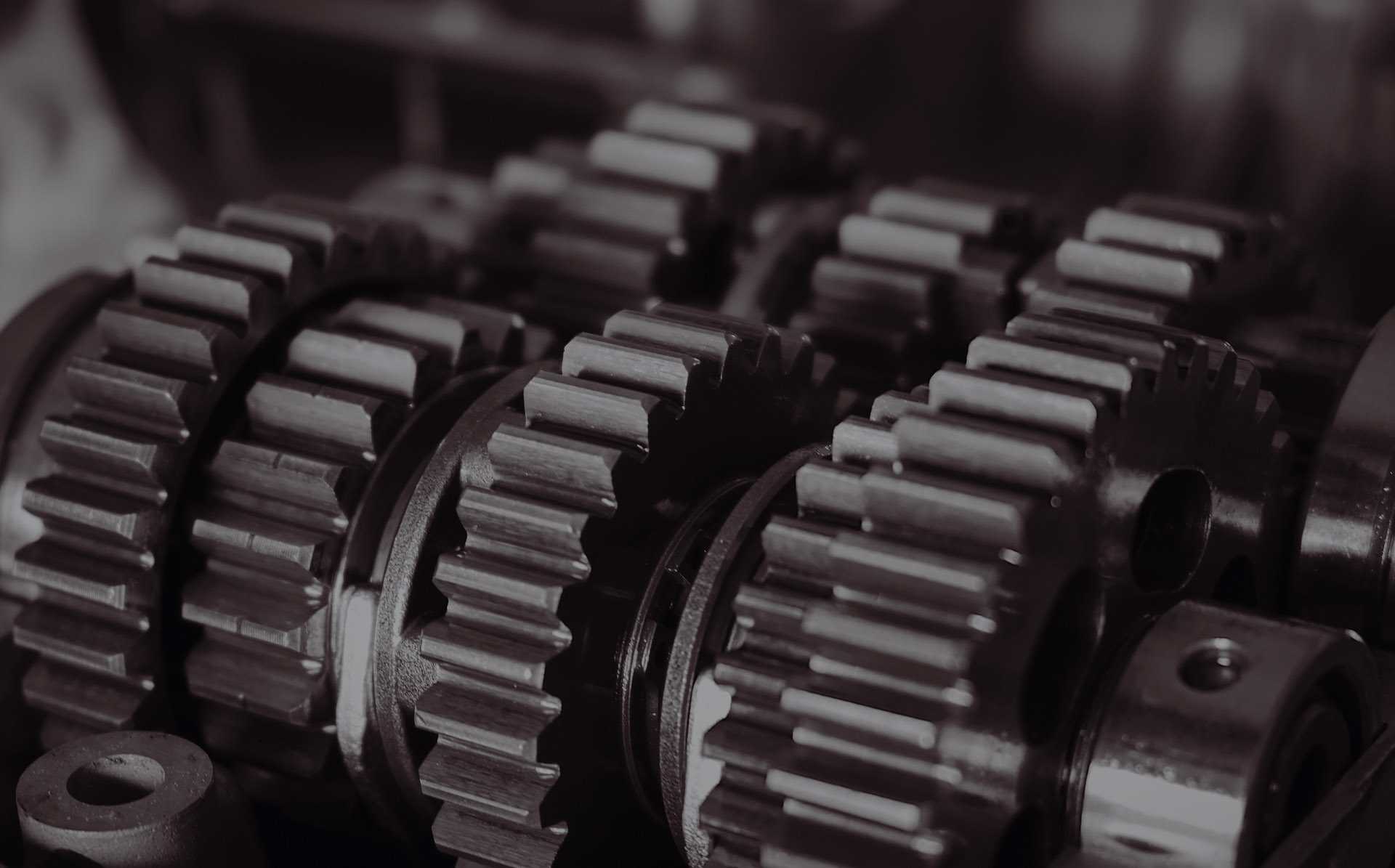
Contacts
-
Russia, Stavropol Territory, Nevinnomyssk, st. Nizyaeva, 41
- TEL. +7 (86554) 9-53-17 EXT. 500/504/104/501/506
- info@sweetstech.com